Pori-based RKW Finland manufactures e.g. label films, films for the beverage and horticulture industry, as well as valve sacks and roof underlayments. Master electrician Sauli Laine has been working with plastic processing for over 40 years. He was also responsible for the recent winder automation project.
“The main focus of the project was clear. The user interface and control system had to be replaced to match the modern needs “, summarizes Sauli.
Tomi Ruohomaa, operations manager, adds that the need for the modernization project became acute.
“The machine had reached a critical age. Spare parts and support were practically no longer available. The line was being upgraded anyway, so we decided to modernize the winder at the same time,” says Tomi. “We compared the offerings both in terms of price and experience. In the end, we chose Extron as the project implementer.”
Tomi states that Extron’s clearest strengths compared to others were experience and the history of manufacturing their own winding equipment.
“They also had the best process understanding”, adds Sauli. “That was a significant factor. Maybe they weren’t the cheapest option, but the quality matched the price.”
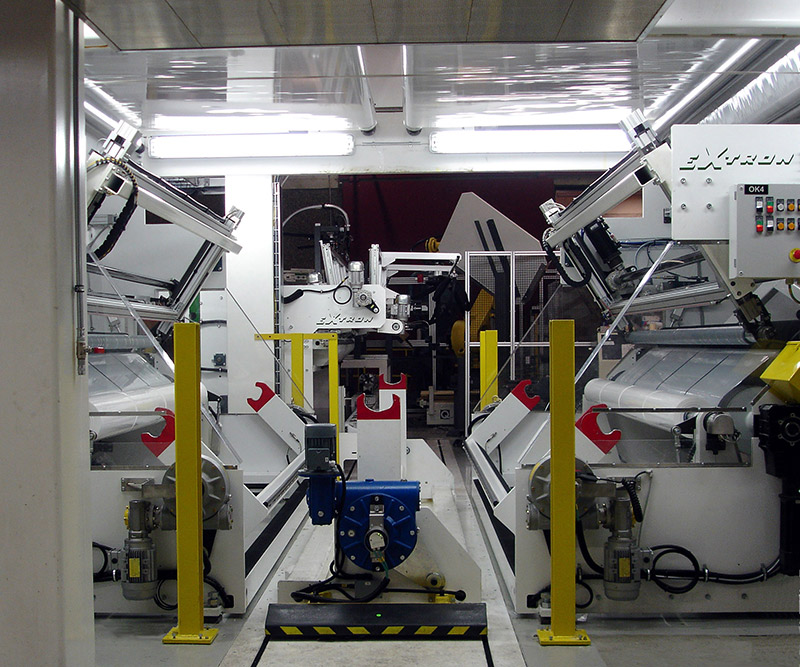
Smooth progress despite the component challenges
Tomi says the project progressed as agreed, from the scheduling to the post-installation training.
“Communication was very easy and clear. It was also great to be able to communicate in our own language. At the very beginning, there were minor misunderstandings regarding the content of the offer, but in the end, it was also agreed upon nicely,” Tomi praises.
Sauli agrees.
“Everything went according to plan, and we were able to stay out of the way. Extron’s professionals had already made the initial preparations in the unit. They delivered the new automation and electrical components pre-installed on an assembly plate that fitted straight to the existing control cabinet. The whole project was well-planned and prepared, and everything went smoothly. They did what they promised and in the agreed schedule”, Sauli sums up.
Perhaps the biggest challenge of the project was the poor availability of components. Anticipation and preparation play an even bigger role in today’s world.
“Sometimes we even tried to hunt for parts in cooperation, with Extron using their own channels and us using ours. In addition, we alerted another operator of the upgrading project for help. In the end, however, Extron’s networks worked the fastest and they got the parts. Delays are never desirable, but that’s the name of the game nowadays. We must anticipate as much as possible and mentally prepare ourselves for the fact that everything will take a little longer,” says Tomi.
Successful project has no surprises
In Tomi and Sauli’s opinion, the primary benefit of the winder modernization project is that the availability of spare parts is in order. In addition, technical support is available for both the device and the software.
“We tried to keep the basic functions the same as before, but the user interface has been renewed after fifteen years. Our operators are currently getting used to the new HMI” says Tomi.
“The implementation has been very well supported”, Sauli clarifies. “Extron’s programmer is very committed to how the new user interface is used in the everyday life of our smart operators. The support of experts has been of the utmost importance, as we had to manage for so long with poor availability of spare parts and limited technical advice.”
The functions of the new UI have already been optimized along the way. Both Tomi and Sauli agree that the reliability of the entire equipment improved significantly.
“The modernization of the winding device was an important part of a broader modernization project,” says Sauli. “Success in these projects is measured by the absence of surprises. Extron did its part excellently, and the main contractor didn’t have to re-schedule or re-arrange their plans.”
In Tomi’s opinion, the project was a success and he is looking forward to new collaborations.
“We intend to cooperate with Extron in the future as well. One joint project is already in plans, if the global component situation allows. And the following projects have also been discussed.”
VIRE WINDERS
When safety comes first, VIRE plastic film winders help you meet the highest safety standards with great usability and reliability. With automated winders, you can boost your performance on construction, packaging and food packing Industries.
Meeting request
Do you want to know how to make your plastic production line safer and smarter? Invite us to your factory!
"*" indicates required fields