Successful processes in the plastics industry are driven by knowledge and experience. Data helps to manage ongoing production, analyze past processes and predict future maintenance needs.
Collecting process data is crucial. Data can be collected on every step of every process to help improve operational efficiency. However, data is useless in practice if it cannot be interpreted correctly and applied in practice. No matter how limited or large the process, understanding of the big picture is always improved by interpreting long-term data.
Teemu Vilminko, Maintenance Manager at Röchling Industrial Rusko, says that data is used effectively in their workflow.
– In cooperation with Extron, we have carried out projects for the renewal and modernization of our equipment. Data has been collected on a line-by-line basis and used at various stages of both maintenance and production. The data has made it possible to take a closer look at the steps in the process and to use the information effectively in day-to-day practice, says Vilminko.
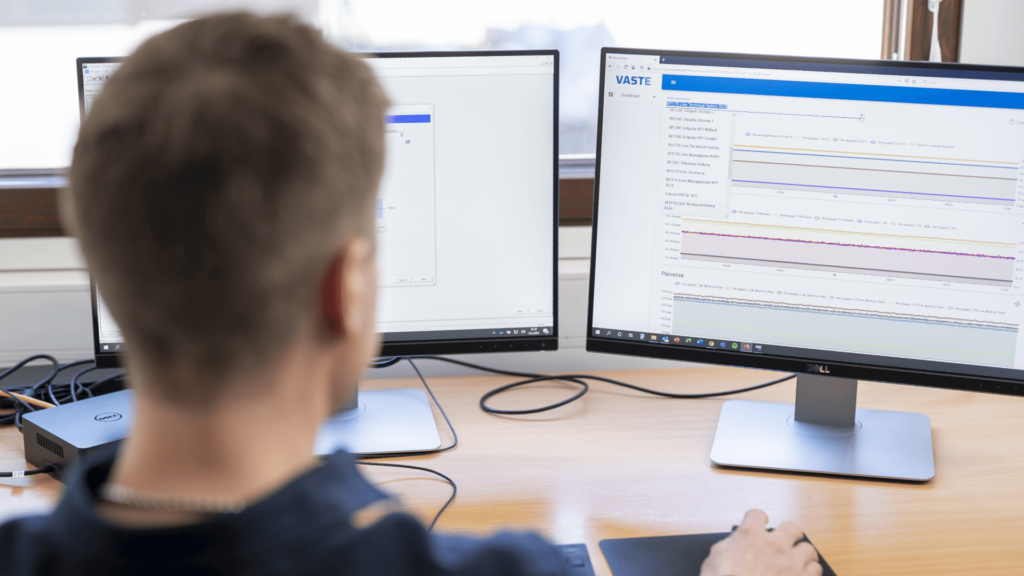
Foresight is the key to success
Predictive maintenance cannot be based on a calendar alone. Data helps to ensure the full operational performance of the line and to maximize its life cycle. Having accurate and timely information about the equipment and the process makes it easier to detect risks and malfunctions. In the event of problems, operators can make solutions based on parameters that have already been proven to work.
– It is always a good thing to be proactive and prepared. Data also allows us to plan and review future operations. It is a great help for our operators’ work planning, Vilminko underlines.
Maximized performance anywhere, anytime
When data is collected directly from the process, no additional interfaces are needed. You can focus on maximizing performance. Extron’s understanding of all stages of an extrusion project and decades of experience with plastics machinery and equipment ensure that the data collected can be used efficiently and easily. For example, energy measurements can be used to achieve optimum production speed and efficiency. Automated reporting of run times, on the other hand, provides up-to-date and accurate data available anywhere, anytime. Processes can also be monitored by a smart device regardless of time and place.
Vilminko is confident that the use of data will only increase in the future.
– Gaining an overall understanding of the process is always easier if the data can be used effectively to support maintenance operations and production planning.