Intelligent design and excellent assembly help us to produce high quality winders and other extrusion units. The detailed testing process, tailored to our customers’ needs, ensures that our products truly meet the highest standards of safety and usability.
The FAT, or Factory Acceptance Test, is carried out when the design and assembly phase is complete and the machine is ready for delivery.
“Many customers want to be sure that the machine works before it is delivered. No one wants an unfinished machine,” says Project Manager Esko Kuivalainen.
Testing is usually carried out at the supplier’s own premises. Some functions can also be tested using simulations. Some tests can only be carried out at the customer’s premises when the delivered equipment is in its real operating environment.
“The main benefits of FAT testing for the customer are to ensure functionality, facilitate commissioning and address contractual issues. An approved test seals the design and assembly phase of a project and ensures that the customer gets exactly the product they ordered,” says Production Manager Jukka Pohjasto.
FAT testing is not limited to winders. Individual elements or larger units can be tested at the customer’s request. According to Jukka, the number of operations and the size of the delivery also influence the extent of testing. For more compact deliveries, testing is often performed by Extron’s own experts and the results are reported back to the customer.
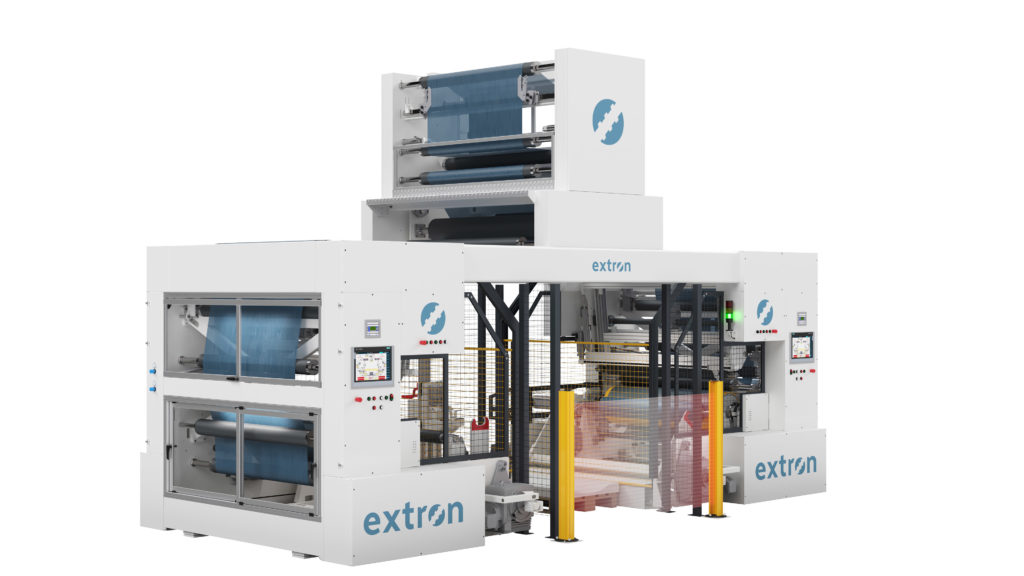
Testing requires preparation and cooperation
Often the tests are routine, but sometimes the content can be more complex. For Jukka and Esko, the most recent extensive test process was the FAT test of a VIRE winder commissioned by a large Central European extrusion equipment manufacturer.
“The testing took two and a half days. The content was tailored in advance according to the customer’s practices. Two weeks before the test, a representative of the customer visited the site to assess the situation and ensure that the test could be carried out on schedule. They indicated that they wanted to simulate the startup of the winder and related functions. The test also verified safety and functionality issues,” says Jukka.
In a test situation, the functionalities were precisely tailored to the customer’s requirements.
“We carried out a simulated test run with roll changes. The delivery also included automated roll and core handling. In the test, this could be done with finished rolls. The change sequence was defined, and the functionality of the change and removal was verified. The test results were as expected. The customer was satisfied and so were we,” says Jukka.
Because the final layout is done at the time of installation, certain items could not be fully tested at Extron’s facilities. Some procedures had to be performed at the customer’s facility.
Esko points out that in addition to functionality, a great deal of attention was paid to safety.
“We wanted to make sure that the equipment met the standards for safety clearances and other safety aspects to eliminate risks to operators and others in the vicinity of the equipment.”
It’s all about safety, flexibility and usability
Jukka says that Extron’s customization and precision in the test phase is especially beneficial in a multi-component project like this.
“We assembled the machine to work exactly as it will be used at our end customer’s facility. This takes resources, but it pays off in the installation phase. Once all the subassemblies have been tested, both parties can be confident that the machine will work and that all the terms of the contract have been met. This is one of Extron’s differentiators in the international market. We are an agile and design-oriented company, which allows us to take a more holistic approach to individual projects and complete projects in-house. We are flexible and make changes according to our customers’ wishes,” Jukka says.
Whatever the industry, the importance of safety and availability will only increase in the future. More and more companies are demanding safer working environments. Standards in the industry are constantly being tightened, but many factories have internal safety standards that go beyond the minimum requirements.
“Security is an important part of quality. Customers want to be sure that safety requirements are met in the test phase, but usability must also be high. Every piece of Extron equipment we ship has to be safe and reliable,” says Jukka.
Increasingly, customers want to be able to examine the equipment and its various functions in the production phase, so they know what they are investing in.
“For us, every step of the process, from design to testing to installation, provides valuable data that allows us to continually develop safer and more user-friendly extrusion equipment,” Jukka concludes.
VIRE WINDERS
When safety comes first, VIRE plastic film winders help you meet the highest safety standards with great usability and reliability. With automated winders, you can boost your performance on construction, packaging and food packing Industries.